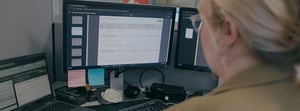
Production Manager
Reports to: VP of Operations
FLSA Status: Full Time, Salary-Exempt
SUMMARY:
The Production Manager is responsible for all of Combi’s North Canton manufacturing operations and manages the operations to ensure that all projects meet functionality, cost, and quality standards and are delivered on time. The Production Manager works across departments to maintain production schedules to manage team assignments and establish daily production goals. The Production Manager monitors every project to identify and resolve issues and implement process improvements. The Production Manager is a “player coach”, developing team members, coaching team members in best practices to provide a safe and efficient work environment and delivering results.
ESSENTIAL FUNCTIONS:
- Provide support and leadership to the manufacturing team; mentoring individual team members, ensuring all training and development needs are addressed and fostering a safe and positive work environment by engaging with employees.
- Drive cross-functional collaboration; plan and coordinate activities concerned with the timely production and quality of company products. Establish production priorities to achieve or exceed revenue, and profitability objectives.
- Implements strategic direction, creates performance metrics, standards, and measurements for the manufacturing operations as well as for departments, teams, and individuals.
- Develop and implement policies and processes to reduce production costs and increase efficiency. Evaluate and report on causes of job costs and margin variances and propose countermeasures. Fully support continuous improvement and quality activities and policies, Work closely with the supply chain and planning teams to create and maintain the production schedules and revenue plan. Drives compliance of production schedules to optimize production efficiency, safety and quality.
- Manage and implement a production plan for all projects; monitor progress and performance against the production plan with project managers; resolve operational problems, and ensure projects are delivered on time, meeting all customer expectations regarding performance and quality.
- Reviews and analyzes production, quality control, maintenance, and operational reports to determine causes of nonconformity with product specifications and operating or production problems.
- Monitors product standards and develops and implements operating methods and procedures designed to eliminate operating problems and improve product quality.
- Consults with engineering personnel related to modification of machines and equipment to improve production and quality of products.
- Ensure that all production processes comply with current safety, OSHA, EPA, quality standards and labor laws.
- Other duties and responsibilities may be assigned as required.
WORK ENVIRONMENT:
This job operates in a professional office setting. This role routinely uses standard office equipment such as computers, phones, scanners, filing cabinets and fax machines.
Physical Demands:
The physical demands described here are representative of those that must be met by an employee to successfully perform the essential functions of this job.
While performing the duties of this job, the employee is frequently required to sit for prolonged periods of time at a desk. Standing and walking to different departments will be required. The employee will need vision to see close, peripheral vision, depth perception and the ability to adjust focus, talk, hear and listen.
Position Type and Expected Hours of Work:
This is a full-time position, working Monday through Friday, 7:30 am to 4:00 pm.
SKILLS and Qualifications:
- Knowledge of OSHA standards and other safety regulations
- Ability to lead and motivate productions teams to achieve objectives.
- Strong skills in assessing situations and making informed, timely decisions.
- Ability to address and resolve workplace conflicts effectively.
- Familiarity with production processes, equipment, and industry-specific practices
- Expertise in scheduling, workflow optimization, and resource allocation.
Education and Experience:
- Bachelor’s degree in business management, industrial engineering, manufacturing or related field
- Proven experience in a production management role, typically 5+ years